Spring diesel maintenance
A diesel engine expert shares a list of jobs to get the iron genny in gear for sailing season
Engine maintenance is rarely at the top of anyone’s list of favorite fitting out chores, but skipping it is hardly a wise option. With luck, major jobs were done before the boat was laid up, so the list of spring jobs is short enough that most DIYers should be able to get through them relatively quickly. And then you can sit back and enjoy the sailing season, knowing that you’ve done what you can to avoid engine problems.
Diesel fuel
Sediment and water in fuel will settle during lay-up, so it’s worthwhile draining a sample from the bottom of the fuel tank, if this is possible. Growth of HUM (bacteria, fungi and yeasts) is generally not a problem in colder climates, but in warmer climates it is a big problem. Using a biocide can help avoid this problem, but checking the fuel (which should have been topped off before hauling or laying up to avoid condensation) is a good idea regardless of the climate you sail in.
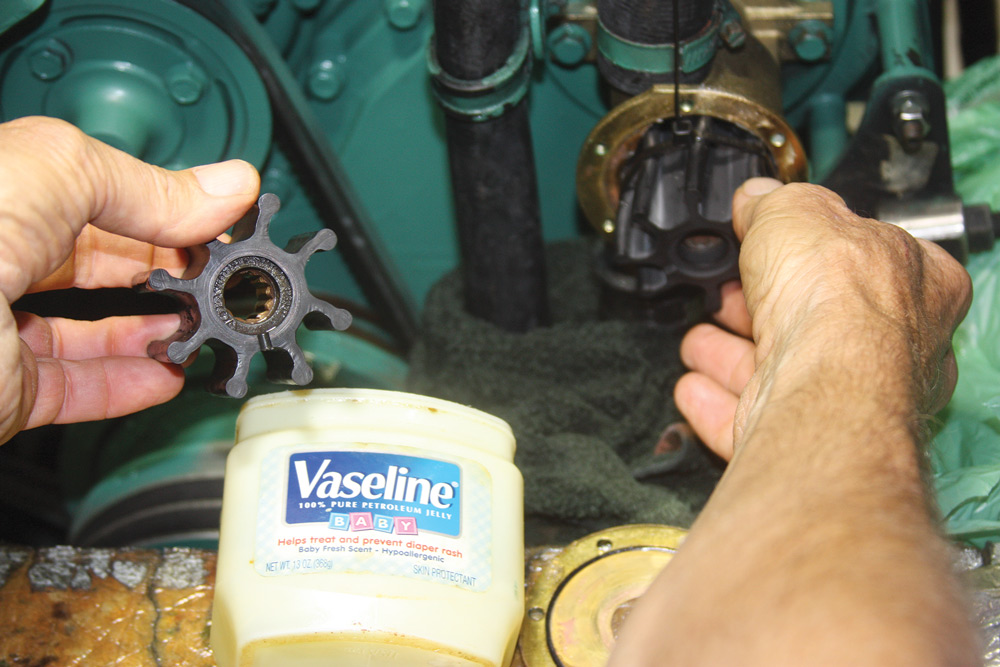
Any water still in the bottom of the primary filter should be drained before start-up.
Fuel-related job list:
1. Drain any sediments and water from the bottom of the tank if possible.
2. Install a new primary fuel filter. Every other year also install a new secondary filter.
3. Check all hose clamps in the fuel circuit.
4. Open fuel valves, including any valve in the fuel return line from engine.
Lubrication
Changing oil and filters removes corrosive acids, which attack the inside of the engine, and helps prevent carbon sludge blocking small oil passages. If this vital task was not done before lay-up, the oil and filter should be changed now.
The best practice is also to change the ATF in the transmission each year. Additives break down over time and the transmission works hard so this is cheap insurance. The ATF certainly should be changed if there has been any evidence of overheating (darkening of the fluid).
Oil-related job list:
1. Change the oil and fuel filters if this hasn’t been done and check the engine oil level.
2. Check the transmission fluid level.
3. Rotate the engine manually or use the starter for a couple of seconds without starting. This will help lubricate bearings before start-up.
Raw water cooling
If the impeller was not removed during lay-up, some of the vanes will be permanently bent (this is called “taking a set”). The pump will still function but will likely be less efficient. A little dishwashing liquid on the impeller makes it easier to twist and insert into the raw water pump housing without cutting or nicking the rubber.
Galvanic corrosion (between dissimilar metals that are electrically connected, by water, or coolant/antifreeze etc.) continues even during lay-up. Anodes should be checked and replaced if they are about 50% consumed. This includes the anode on the propeller shaft, if the vessel was laid-up in the water.
Job list:
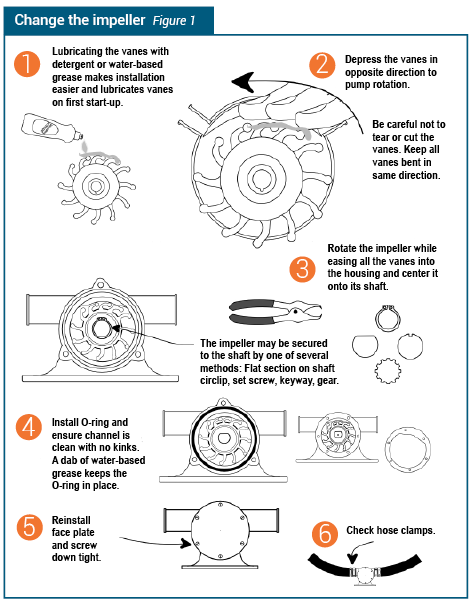
1. Reinstall impeller, or replace if necessary (Figure 1).
2. Check that all seacocks open and close easily. If a seacock that is frozen open cannot be serviced or replaced, it should, at least, be equipped with a wooden plug in case the hose fails. (Best practice at all times).
3. Check hose clamps (and hoses). Temperature changes can cause hose clamps to unfasten.
4. Check anodes in the heat exchanger, header tank, oil cooler, engine block. Replace if they are 50% or more consumed (Figure 2).
5. If vessel was laid up in the water, check the propeller shaft anode.
6. Re-assemble the syphon break, which was flushed in fresh water to remove any scale or salt crystals. Take care to re-assemble it correctly.
7. Reconnect the exhaust manifold, wet exhaust hose and raw water hose into the exhaust riser, if any of these were disconnected.
8. Close the drain on the water-lift muffler.
9. Open the wet exhaust through-hull, if this was sealed to prevent rodents entering the vessel.
Coolant/Antifreeze
1. Check the level of coolant/antifreeze in the head tank or overflow bottle.
Air flow
1. Re-install the air filter if it was removed for cleaning.
2. Open all air intakes to the engine room and check that they are clear of any winter insulation.
Electrical
Sulphates will harden on the plates (this is called sulphation) if a battery was not kept fully charged. This reduces its capacity, even when “fully” charged. The best practice is to load test the battery if there is any doubt about its condition and ability to start the engine throughout the coming season.
Job list:
1. Inspect battery and battery box for any signs of swelling, cracking or spilled battery acid, especially in regions experiencing freezing (Figure 3).
2. Check electrolyte levels and add distilled water if needed.
3. Reconnect battery terminals. Best practice is no more than four terminals to a battery post. Avoid wing nuts as these are prone to vibrating loose.
4. Tighten the belts (alternator, raw water pump).
5. Switch bilge pump to Auto and lift the arm on the float switch to activate and check the pump.
Drive train
With the transmission in neutral, the propeller shaft should turn easily and smoothly.
Out of the water
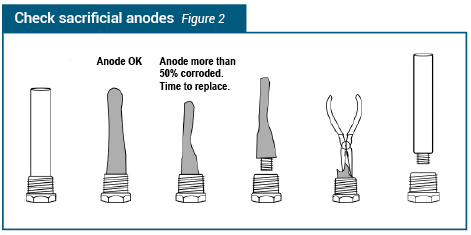
1. Inspect the strut and cutlass bearing and change the bearing if loose or damaged.
2. Inspect the propeller shaft anode and replace if close to 50% consumed (Figure 2).
3. Inspect the propeller, prop nuts and cotter pin.
4. Check control cables (throttle, gear and stop) are securely attached (Figure 4).
5. Some dripless lip-seal stern glands need to be greased each year. Check the manual for maintenance schedules.
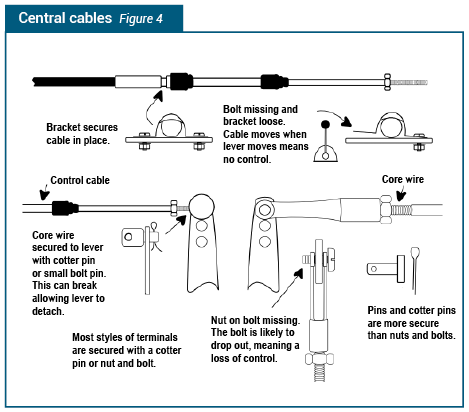
In the water
Items needing attention just before and after engine start include:
1. Open raw water seacock.
2. Raw water strainer may need to be primed, if above the waterline.
3. Start engine and check the raw water flowing from exhaust. If not, the strainer may be airlocked. Unscrew the top slowly to allow water to flow up from the seacock, then retighten.
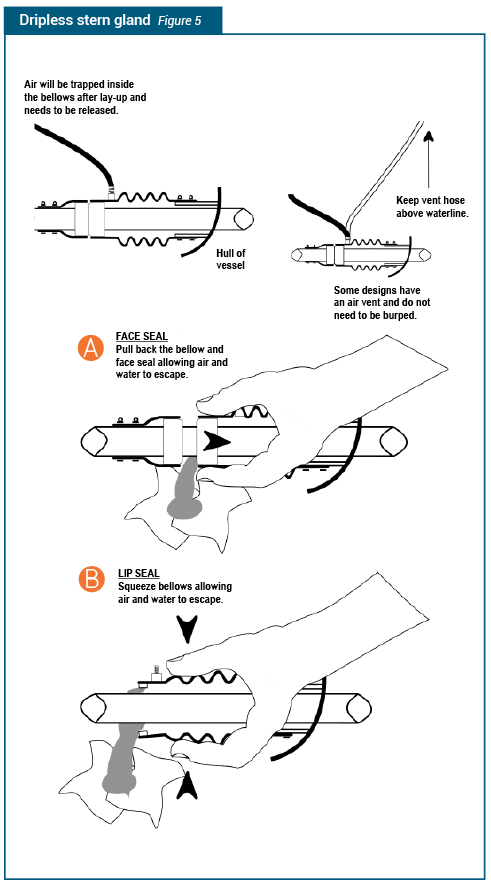
4. Check that the alternator is charging.
5. Adjust traditional stuffing box packing until the box drips approximately once every 10 seconds and not at all when the shaft is still.
6. Dripless stern glands must be “burped” to remove trapped air from the bellows if there is no air vent (small open-ended hose coming from the bellows to above the heeled waterline). Trapped air will cause the seal to overheat and fail (Figure 5).
7. Check seacocks and the water strainer for leaks.
8. Before leaving the dock, verify that the boat responds to all movement of engine controls (forward, aft, neutral, throttle and engine stop).
Dennison Berwick is author of Marine Diesel Basics 1, Maintenance, Lay-up, Winter Protection, Tropical Storage, Spring Recommission. The book is the first visual guide to marine diesel systems on recreational vessels. He lives aboard Oceandrifter, a 36-foot Chevrier.
Comments