Inflatable life jacket maintenance
The following multi-tiered approach to maintenance stems from recommendations from manufacturers and the U.S. Coast Guard, and covers both hydrostatic (pressure sensing) and bobbin type (water soluble) auto inflation systems.
The European Emergency Sea Rescue Equipment Trade Federation recommends a 10-year lifespan for inflatable PFDs and that’s providing the device is professionally serviced at least every two years. There’s a proviso that after 10 years, annual inspection may extend the lifespan to 14 years. After that, a life jacket should be removed from service due to “the possibility of delamination of fabrics and floatation bladder and the degradation of the inflation system.”
Prior to wearing your inflatable PFD
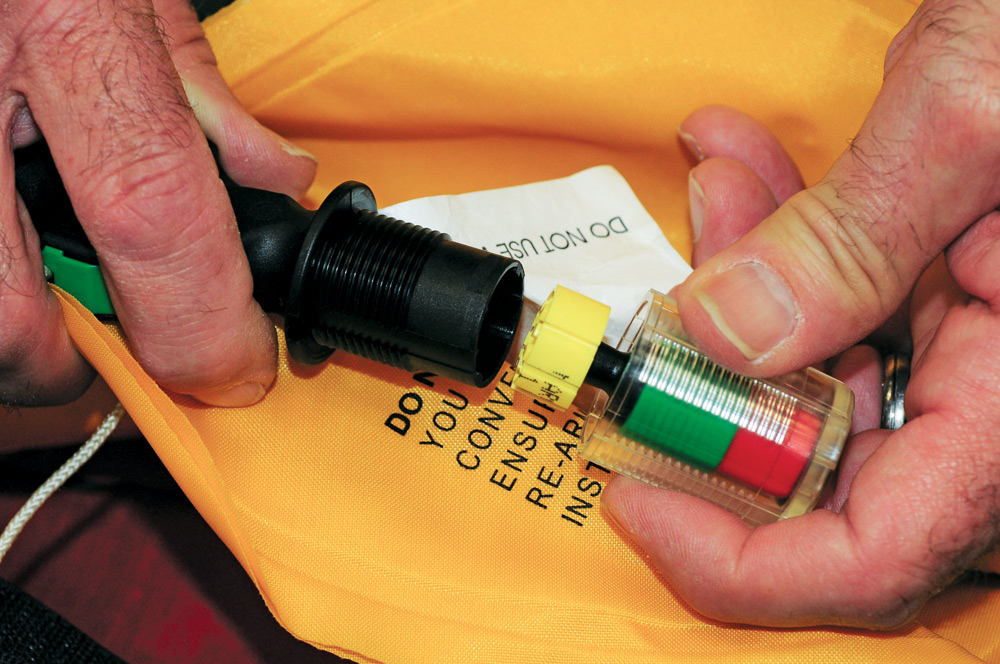
1. Make sure that the indicator(s) are green and, if the unit uses a hydrostatic inflator, that it’s within its expiration date.
2. Check the oral inflation tube by separating the Velcro or unzipping the cover and make sure that the dust cap is on the end of the tube. If an AIS beacon is fitted, it should be secured to the lower portion of the tube.
3. Confirm that the manual inflation pull tab is easily accessible.
4. Make sure all Velcro closures are aligned and sealed and zipper tabs are in the correct location. Check harness and leg/crotch strap alignment and eliminate twists.
5. Inspect the cover for signs of abrasion, chemical damage and stitching failure.
Every two months
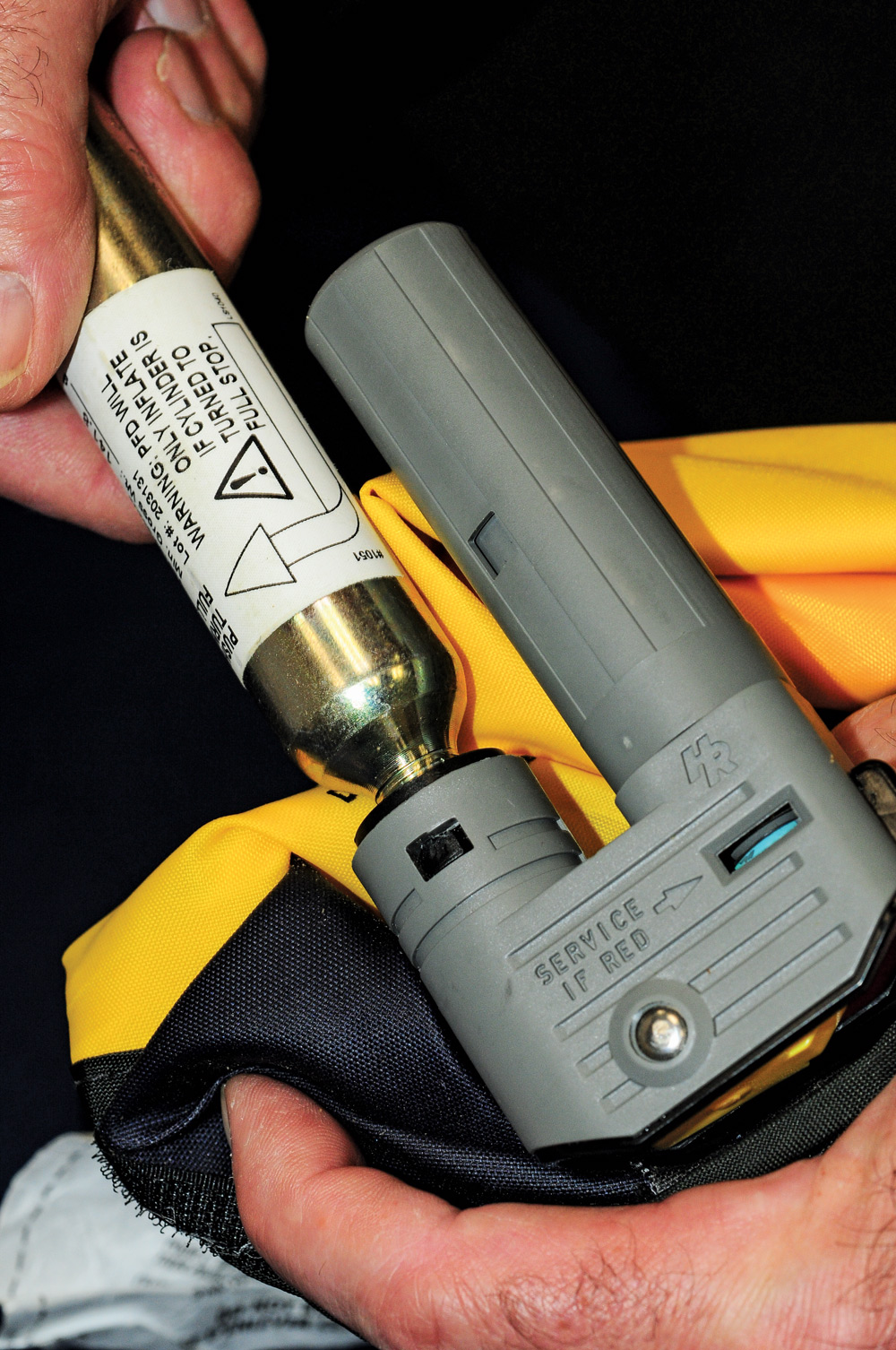
1. Inflate orally and leave for 12 to 18 hours. There should be no change in firmness. If a noticeable change occurs most manufacturers recommend returning the unit for repair or replacement. Those in remote locations may opt to test for leaks using a wet soapy sponge or partial bathtub immersion, taking care not to immerse the auto inflation system. Seam leaks and inflation tube attachment failures require manufacturer’s attention.
2. Check the valve at the end of the oral inflation tube by immersing it in water, taking care to keep the auto inflator dry. If bubbles appear, deflate the jacket and orally re-inflate. This process often improves the valve’s seating and stops the leak. If it continues, it requires a return to the manufacturer.
3. Visually inspect for signs of fabric deterioration.
After CO2 inflation (in water use)
1. Dry (opened up) in as low a humidity situation as possible.
2. Re-arm inflator according to manufacturer’s step-by-step.
3. If it’s a hydrostatic system, after installing a new inflator, orally fill and check air retention 12 to 18 hours later.
Annual Inspection
1. Open up and hand wash with mild soap and rinse (keep the inflator away from water) air dry on plastic hanger.
2. Examine all webbing and cover material and check stitching. Inspect the bladder for chemical deterioration, delamination, seam separation and abrasion.
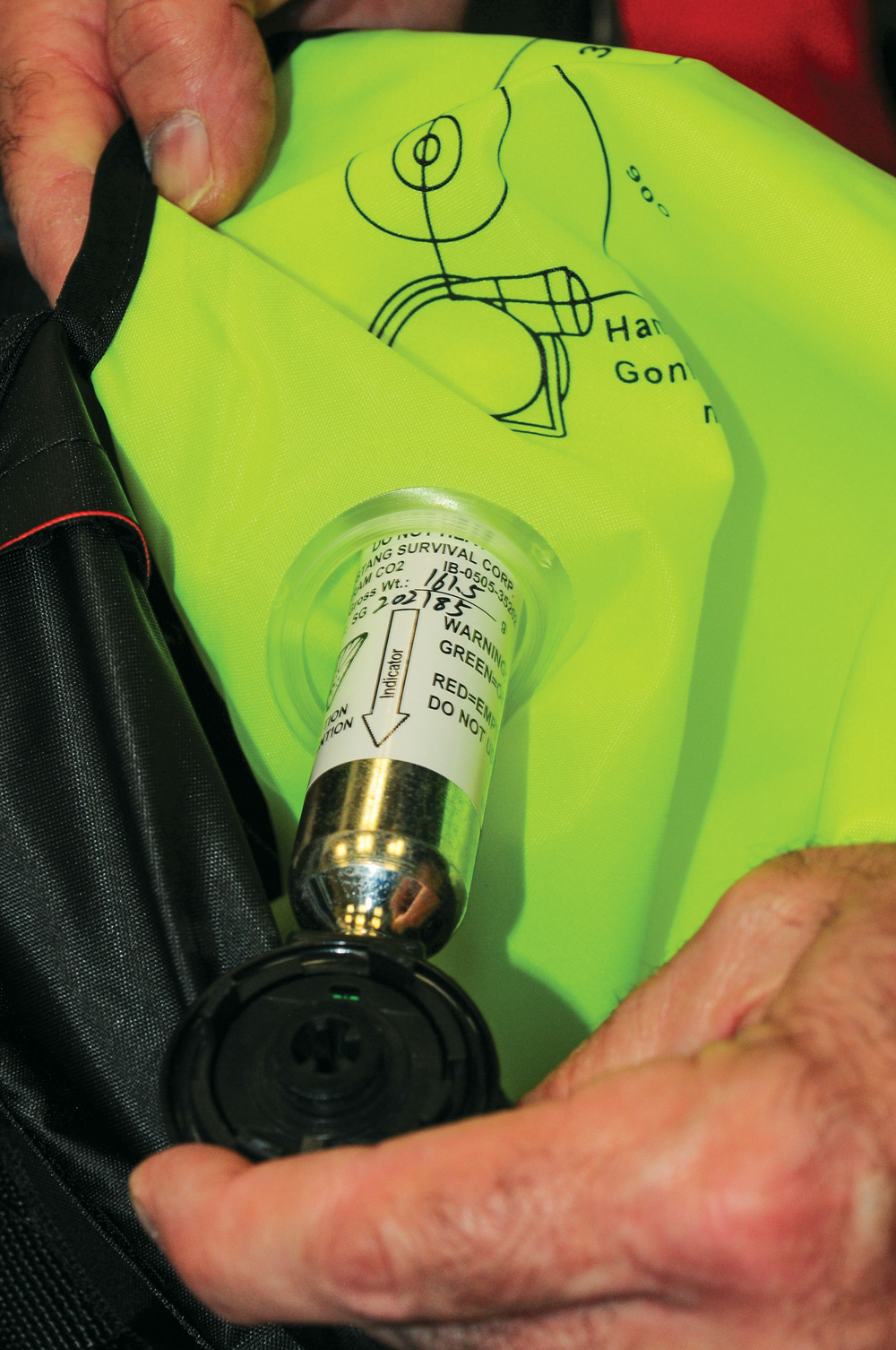
3. Check all metal parts for corrosion.
4. Repeat two-month leak and inflation tube tests.
5. Check the date on the strobe (replace batteries), test whistle.
6. Repack according to manufacturer’s instructions.
Manufacturers’ information:
Mustang Survival, www.mustangsurvival.com; Spinlock, www.spinlock.co.uk; West Marine, www.westmarine.com; Secumar, www.secumar.com; Halkey-Roberts inflators, www.halkeyroberts.com; UML, www.uml.co.uk; Hammar inflators, www.cmhammar.com
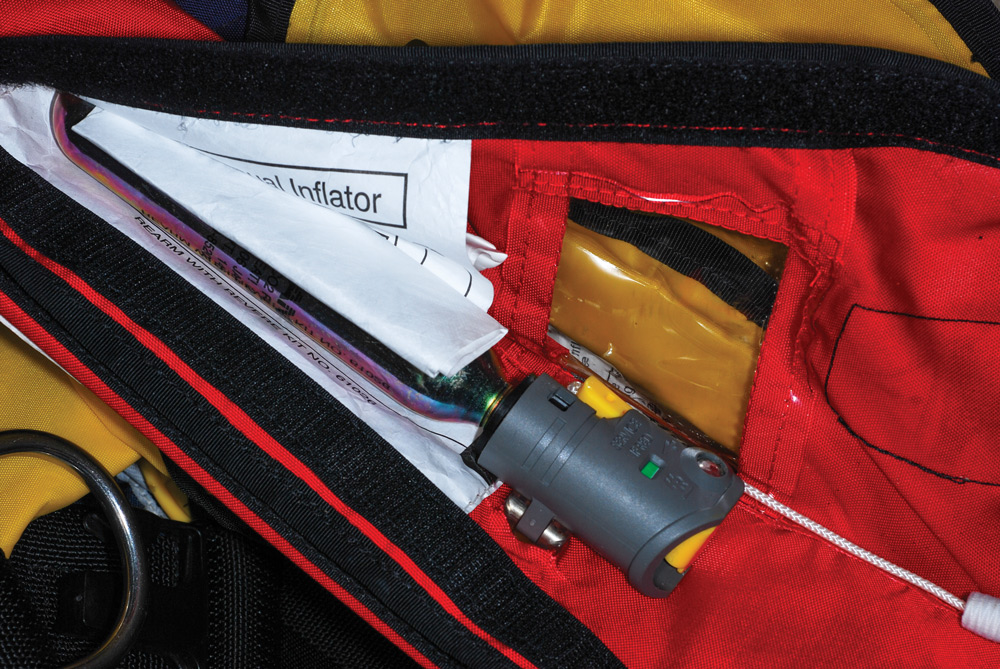
Comments